SLS PA12

SLS PA12
Durable, heat-resistant nylon material for detailed, functional prototypes and stable end components.
Available colors
Available post-processing
Gallery
Suitable for
- Functional prototypes and final components
- Applications in the automotive and electronics sectors
- Complex geometries
- Moving parts such as gear wheels
Unsuitable for
- Large models
- Permanent UV exposure and outdoor applications (possible with acrylic lacquer)
- Models with fine details and a smooth surface
Additional information
This material is extremely versatile and is suitable for a wide range of applications - from iPhone cases to jewelry and remote-controlled quadrocopters to industrial parts. In thin layers, it is flexible enough for hinges and springs; in thicker layers, it is strong enough for load-bearing structural elements.
The flexibility depends on the structure and design of the model: the thicker a component, the less flexible it becomes. A spring made of 1 mm thick wire can be easily compressed and stretched, while a spring made of 3 mm thick wire is significantly stiffer and does not give way even when dropped from a great height.
Although details are visible from 0.4 mm, text that is raised by at least 0.6 mm is particularly clear. For sharper text and more precise embossing, it is advisable to increase the thickness to 0.6 mm.

Minimum wall thickness with supported wall
A supported wall is one that is connected to other walls on two or more sides.

Minimum wall thickness for unsupported wall
An unsupported wall is one that is connected to other walls on less than two sides.

Minimum supported wire thickness with support structure
A wire is a feature whose length is more than five times its width. A supported wire is connected to walls on both sides.

Minimum supported wire thickness without support structure
A wire is a feature whose length is more than five times its width. An unsupported wire is connected to walls on less than two sides.

Minimum hole diameter
The precision of a hole depends not only on its diameter, but also on the thickness of the wall in which it is printed. The thicker the wall, the less accurate the hole can be. For holes that go all the way through, it must also be ensured that there is a clear line of sight so that all excess material can be removed during post-processing.

Minimal raised detail
A detail is a feature whose length is less than twice its width. The minimum size of details is determined by the printer resolution. If the detail dimensions are below this minimum, the printer may not be able to reproduce them accurately. Details that are too small can also be smoothed out during polishing and thus disappear.
To ensure that details are clearly displayed, they should be larger than the specified minimum. We may not be able to print products with details below the minimum size as the end result will not match your design. If your product contains smaller details, try to enlarge them, remove them or choose a material with finer detail reproduction.
Minimal engraved detail
A detail is a feature whose length is less than twice its width. Engraved or recessed details are those that go into a surface.

Minimum distance between components
The distance is the space between two parts, walls or wires. To achieve a successful print result, the gap between parts, walls and wires should be greater than the specified minimum. If the distance is too small, it may help to increase the gap or connect the parts or features if their independence is not necessary. Alternatively, a material with a smaller minimum gap can be selected.

Included parts possible?
Sometimes interlocking or moving parts cannot be printed because the supports inside the cross-section cannot be removed.

Support structures needed?
As each layer must build on the previous one, some materials at angles greater than 45 degrees usually require supports to be printed along with the design. Supports are not inherently detrimental to your design, but they increase the complexity of the printing process and result in a less smooth surface on overhanging parts.
Properties
Weather resistant

Heat resistant

Elastic

High strength

Chemically resistant

Biodegradable
Technical data sheet
SLS (selective laser sintering)
How it works:In the SLS process, powdered material, usually nylon, is melted layer by layer into the desired shape using a laser. The laser heats the selected areas of the powder so that it sinteres into a solid object. After each layer, fresh powder is applied, which also serves as a support for complex geometries.
Advantages of SLS:
- No support structures required: The unsintered powder serves as a support material, making complex geometries possible without any problems.
- Durable and stable: SLS prints are robust and resistant, ideal for functional components.
Do you have any questions?
If you have any questions or would like a customized offer, please feel free to contact us. We usually reply on the same working day.
Swiss3D - Your reliable print-on-demand 3D printing service for high-quality and customized 3D prints in Switzerland.
Follow us -
Aktuelle Auslastung: Moderat – Ihre 3D-Druck-Aufträge werden zeitnah bearbeitet
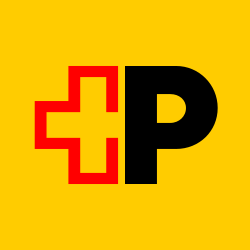
Aktuelle Auslastung: Hoch – es kann zu geringen Lieferverzögerungen kommen
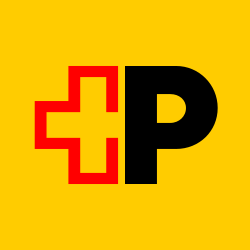
Copyright © 2025 - Swiss3D GmbH






